In recent years, energy saving has become a hot topic in new automotive technologies and trends. Looking back at the past 20 years, the electronicization of cars is mainly driven by drivers for more comfortable and luxurious equipment, such as electric windows, electric sunroofs and convertible covers, high-end audio equipment, electric seats, air conditioning or electric hydraulic power steering systems, etc. Driven by the desire, these devices all increase the demand for semiconductors and electronic parts in automobiles. Now, the primary goal of electronic car design has been different. Although luxury equipment and better driving functions are still important for cars, now and for the foreseeable future, most of the electronic systems used in contemporary cars are also to reduce emissions, improve fuel efficiency, and reduce the power consumption of in-vehicle systems. As the driving force.
The best way to achieve this goal is to use more efficient and smarter electronic systems to replace the car's mechanical and hydraulic systems. A typical example is to replace hydraulic or electrohydraulic systems with electric steering systems; electric motor drives instead of continuously running belt drive systems, like air conditioner compressors, turbo chargers, or other pumps and fans. Even some lighting applications, such as energy-saving "high intensity gas discharge lamps" (HID) or LED lamps, are used to replace traditional bulbs that lack efficiency. Eventually, the internal combustion engine will also be replaced by an efficient electric motor, as we now see in the power systems of hybrid and electric vehicles.
Automotive electronics has also made these semiconductor suppliers of International Rectifier (IR) to develop high-efficiency power management solutions, so as to maximize the energy efficiency of these applications. IR's advanced power management solution combines very advanced silicon technology and revolutionary new packaging technology to improve both the performance and durability of automotive systems. Especially in packaging, we bring innovative solutions to system designers, as well as new ways to design ECUs, motor drives and power supplies.
Today's silicon technology enables very good switching, such as the latest channel MOSFETs and IGBTs. However, related packaging technologies often use very conservative soldering methods to attach silicon chips to substrates or lead frames and connect their surfaces with bonding wires. As early as 2002, IR has begun to develop new connection interfaces. It is hoped that through simple packaging, our best silicon technology can be connected to power circuits, and the interface between current and heat flow is minimized. The end result is that we have developed DirectFET technology that eliminates bond wires. The realization of this technology relies on the front metal of the silicon switch being solderable, so that the MOSFET surrounded by a simple metal shell can be directly soldered to the printed circuit board. The concepts shown in Figures 1 and 2 are mainly simple in design, minimize materials and interfaces, and the most special is that there is no need to use bonding wires to achieve the best power and temperature performance. In addition, this concept can also improve the quality and reliability of automotive systems because it eliminates the dominant failure mode in the automotive power cycle: the so-called bond wire detachment.
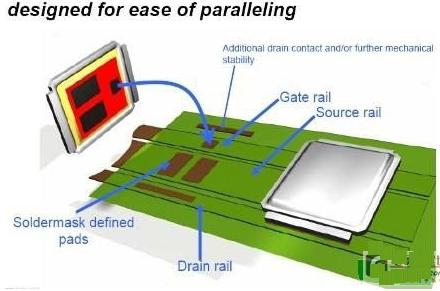
Figure 1: DirectFET soldered on the PCB.
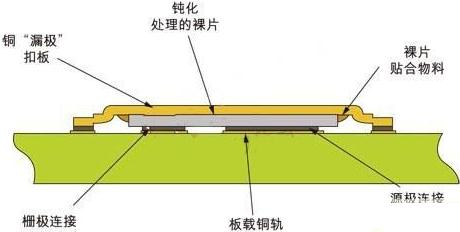
Figure 2: Cross-section of DirectFET: The temperature and power interface of the silicon chip is minimized, and the power and temperature performance is far beyond the standard package with bonding wires.
Ipad Screen Protector,Ipad Screen Protectors,Best Ipad Screen Protectors,Tablet Screen Protectors For Ipad
Guangdong Magic Electronic Limited , https://www.magicmax.cc